泛娱乐建设焊材强国 这座“金桥”飞架新赛道
2023-12-20 18:20:02
admin
攻克“卡脖子”技术
在过去的很长一段时间,涉及国家能源安全的10万立方米以上大型石油储罐建设,所需的气电立焊药芯焊丝一直依赖进口。
为打破国外对于该产品的长期垄断,解决我国大型石油储罐建设最后一项“卡脖子”技术,确保石油战略储备资源的安全,金桥焊材牵头立项,并于2021年12月完成了大型储罐高强钢用气电立焊药芯焊丝国产化。
对于这样“一种高强度高韧性气电立焊药芯焊丝及制备方法”, 中国焊接协会在出具“推荐意见”时,给予了高度评价:
“本专利产品通过了天津市高新技术成果转化中心和中国石油工程建设协会联合组织的科技成果鉴定,部分指标超过进口同类产品,达到国际先进水平。 ”
“本专利产品使我国大型石油储罐建设实现了完全国产化,对提升石油储罐工程建设行业自主权及高质量发展,具有重要的社会意义和经济意义。”
目前,本专利产品已替代了进口产品,在中石化、中石油、中海油大型石油储罐商储、国储项目上实现了批量应用,累计焊接10万m³以上原油储罐超过300座。
服从国家发展战略,攻克“卡脖子”技术,拿下“卡脖子”产品,以自主可控、高质量的供给,确保国内焊接产业链和供应链的安全,早已被金桥焊材这家国家科技创新示范企业,视为誓夺焊材世界创新冠军的关键一战。
仅是最近几年,金桥焊材依托国家级企业技术中心、院士工作站、博士后科研工作站、天津市企业重点实验室等平台的科技支撑,借助完善的产、学、研、用创新机制,坚持原始创新、集成创新、开放创新一体设计,做到创新链、产业链、人才链一体部署,先后承担了国家工业强基工程、科创中国等九个国家级、省部级科技项目,攻克了多项“卡脖子”技术,拿下了多个“卡脖子”产品,逐个打破外国对海工、石油管线、锅炉压力容器、桥梁等重点领域的垄断。
深耕管线焊材领域,金桥焊材率先研发JC-29Ni1、JC-30、JC-80管道用自保护药芯焊丝,满足了石油天然气X70 X80管线钢的半自动焊接,在西气东输二、三线等国家重点工程大显身手,成功填补了国内空白。
随着管线焊接技术的不断发展,金桥焊材聚焦国家战略需要,先于行业推出了管线钢用全自动焊药芯焊丝、X65-X80管道全自动焊丝产品,并成功应用于漠大二线、闽粤支干线等国家工程。
中国油气管道焊接的“卡脖子”问题,由此得到破解。
涵盖焊条、药芯焊丝、埋弧药芯焊丝及焊剂四类产品的3Ni耐海洋环境大气腐蚀系列焊材,以其填补国内空白,实现了海工用焊材国产化,打破了进口焊材对我国海工走向深水的制约。
低镍800MPa级高强高韧系列特种焊接材料,填补了国内低镍E690级高强钢焊材空白,圆满完成国家级强基工程“高强高韧特种焊接材料实施方案项目”。
奔跑在争夺焊材世界创新冠军的新赛道上,金桥焊材以其高端化的自主创新, 现已取得授权专利500余项,其中发明专利100余项;参与制定国家标准29项、行业标准3项、团体标准12项;荣获中国好技术、国家重点新产品、天津市重点新产品、天津市专精特新产品、天津市专利金奖等数十个奖项。
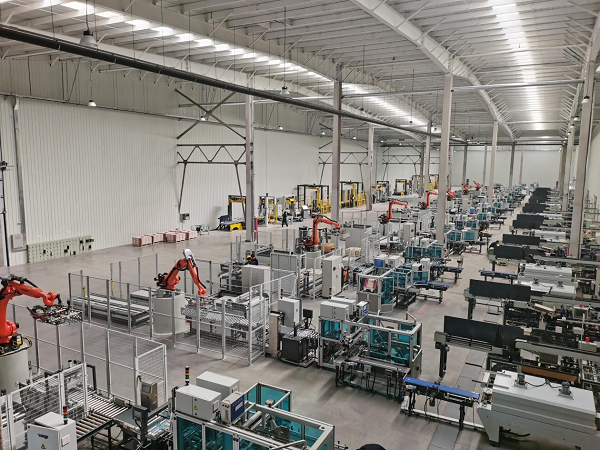
焊材智能制造车间
树立智造应用新标杆
2022年3月,中国焊材制造业的第一家智能工厂—金桥高端焊材智能制造工厂,在天津经济技术开发区正式投产。
该项目投资8亿元人民币,占地区13.3万平方米,于2020年4月开工建设。该项目投产后,可年产高端焊材40万吨,增加年产值约20亿元,人工成本大幅降低,土地综合使用效率提升4~5倍,碳排放几近于零。
以其数字化的典型应用场景及由此带来了显著应用成效,这座高端焊材智能制造工厂,不仅开启了中国焊材产业数字化的先河,也为打造自主可控、安全可靠、竞争力强的现代化焊材产业体系,树立起智造应用新标杆。
作为在新赛道上誓夺焊材世界创新冠军的又一场对决,金桥焊材为打造国际先进、行业领先的数字化焊材生产线,并使该项目成为中国焊材业智造的应用新标杆,立足自主创新,借助联合创新,攻克了焊材制造设备互联与系统集成等重大制造工艺与技术难题,辅以生产线数据监测与采集控制系统,实现了数据自动采集、设备自动控制、参数自动调节、信号自动预警,开创了集自动化、信息化和绿色制造为一体的焊材生产新模式。
这一中国“焊材生产新模式”的诞生,还得益于“国家工业强基任务中标单位”的厚实先期铺垫。按照《金桥焊材智能制造实施总体规划》,早在中国焊材制造业第一家智能工厂启动之前,他们就已全方位、高水平、快节奏的推进数字化转型。
一是加快从自动化向信息化的转变,提速两化融合,在企业网络、MES生产系统、供销管理平台、WMS仓储管理系统等方面推进信息化建设。加速推广自动化生产设备在各厂区的应用,进一步提高高效设备和自动化生产设备占比,形成国内不同地域焊材生产制造集群,为焊材行业的智能制造奠定基础。
二是加快工业互联网平台建设,对新厂区的网络按照数据网络、监控网络和工业生产网络进行三网规划。持续对老厂区的网络进行升级改造,优化线路路径,满足各类办公及管理系统对网络的要求。新车间建设时,同步完成底层数据的采集,结合生产情况以及数据提取实际需求,配套MES系统。上线供销管理平台、资产管理平台,实现客户在线采买、供应商在线管理以及物料信息化。推进仓储信息化建设,跟踪仓储物流发货全过程。
基于如此厚实的先期铺垫,这座高端焊材智能制造工厂,才能将物联网手段实际应用到生产全过程,实现工业总线、条码扫描、标签感应、移动PDA、PLC控制等技术有机融合,并以“机器人+”应用新标杆,成功入选国家工信部“数控一代”焊接卷案例集,大力向行业进行推广。
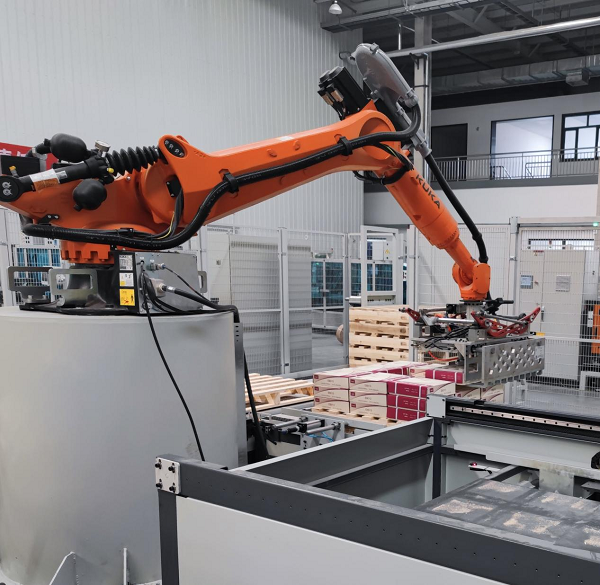
机械手码盘
打造绿色制造新样本
从生产线、基础设施、能源利用、碳汇资源等多个维度进行合成创新,金桥焊材已率先构建起高效、清洁、低碳、循环的绿色制造新模式。
仅是2022年3月投产的金桥高端焊材智能制造工厂,利用绿能发电,打造“风光组合”,预计年光伏发电量1390万kWh,风电发电量1500万kWh,可实现近零碳排放。
绿色,当是焊材强国的底色。唯有践行绿色发展理念,采用新技术、新工艺、新材料,以全方位、全流程的绿色创新,才能实现“双碳”目标,才能把中国早日建成真正意义上的焊材强国。
在绿色赛道上跑出“加速度”,就是金桥焊材这家国家级绿色工厂,在志夺焊材世界创新冠军路上的又一项比拼。
为打造绿色制造样本,早在10年前,金桥焊材就启动了“绿色制造工程”。
他们在天津市科委“领军小巨人企业重大专项”的支持下,从改造传统生产工艺入手,组织专业团队集中三年的时间进行技术攻关,用物理除锈取代了盘条酸洗除锈,并开发出不用硼砂也能保证焊丝正常拉拔的新工艺,终结了焊丝在生产过程中用酸除锈的历史,以每年减少近万吨的废酸量,彻底解决了焊丝拉拔过程中造成的酸对环境的污染。
他们自主研发新型拉丝模具——CRD辊模,避免了润滑粉的使用,再无扬尘及难闻气味。
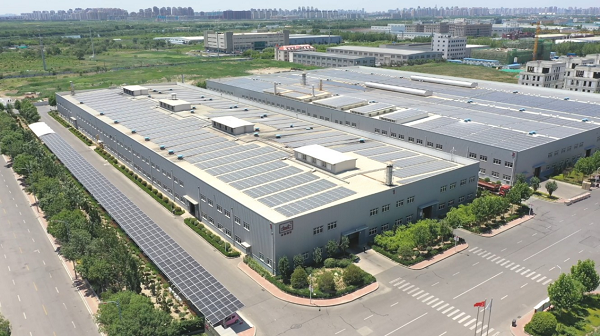
车间屋顶光伏发电
在焊条药皮配粉工艺上,将半机械化配粉升级为智能化自动配粉,并通过管道直接输送到电焊条压涂生产线,彻底根治了焊条配粉过程中的粉尘污染。
为从根本上破解了燃煤锅炉对空气的污染难题,他们斥资1.2亿元,拆除了原有的17台工业燃煤锅炉,重新安装了110台燃气机,全部采用天然气能源烘干电焊条,并通过远传数据采集、实时监控,确保能源的高效合理使用。仅这一项,每年减少原煤4万吨,折标准煤约2.86万吨,可减排二氧化碳7.5万吨。
为让“金桥”成为彻底的“无煤”企业,他们还实施了多个利用新型能源取代燃煤的项目。他们曾投资100多万元,用太阳能取代燃煤给水加温,为产品加热工序提供热水,并加装水源热泵进行余热回收循环利用。他们还通过合同能源管理模式实施了光伏发电项目。截止目前,他们已累积装机功率为31.18MW,年可使用光伏电约3200万千瓦时,相当于少耗标准煤约3900吨,年减排二氧化碳超过1万吨。
“金桥”版的“绿色制造样本”,不仅包括全流程绿色生产,还包括焊材的全部“绿化”。 他们自主研制的多系列绿色环保无镀铜气保实心焊丝、埋弧焊丝,从根本上杜绝了酸碱等化学品对环境的污染。对那些仍然热销的传统焊材,他们也进行了全面的技术改造,经检验达到环保要求后才又重新投放市场。
去年,中国焊材制造业的第一家智能工厂—金桥高端焊材智能制造工厂的建成投产,不仅为中国焊材业树立起智造应用新标杆,更是为中国焊材业打造了最新版的“绿色制造样本”。